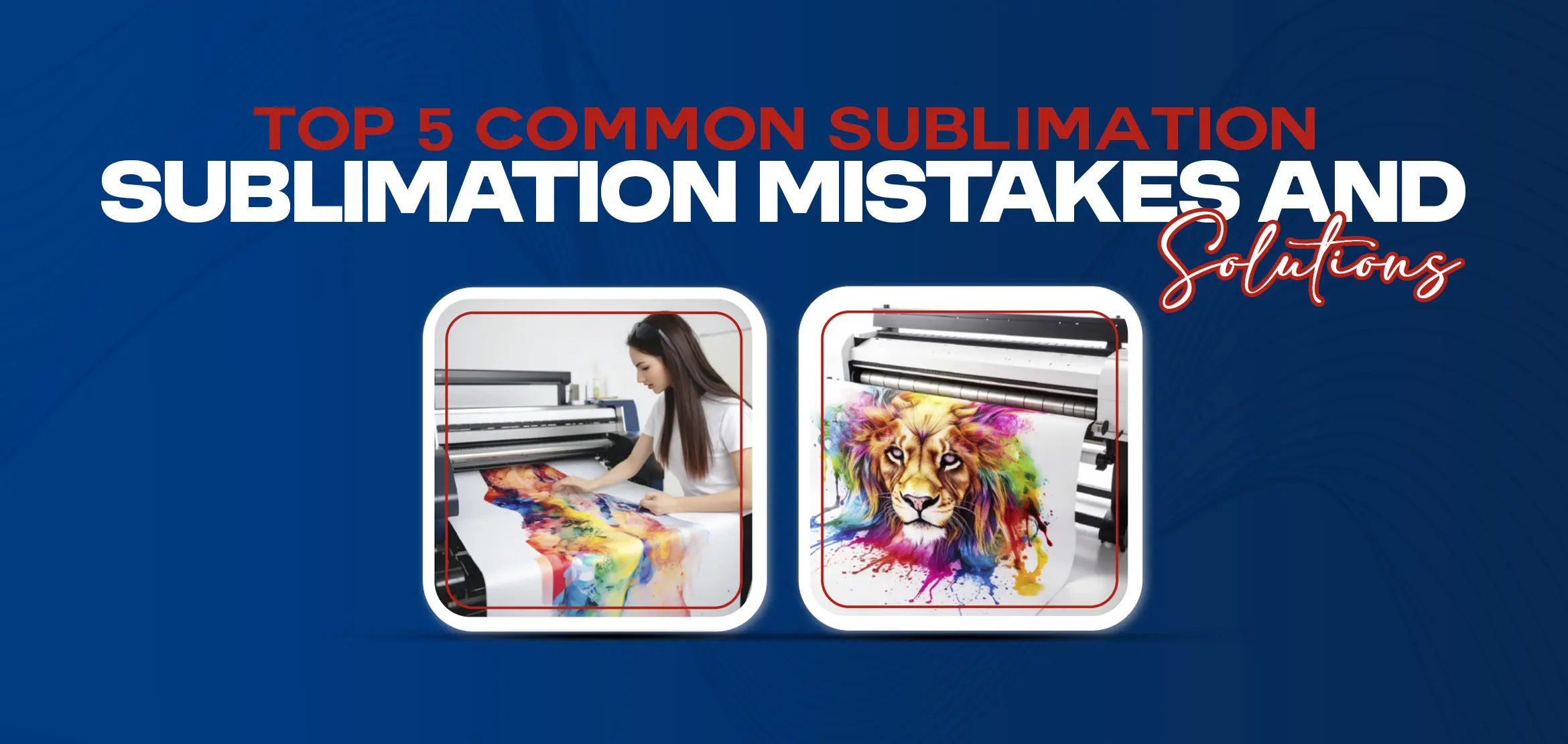
Top 5 Common Sublimation Mistakes and Solutions
Table Of Content
- 1. Poor Image Quality
- Sublimation Mistake:
- 2. Incorrect Heat Press Settings
- Sublimation Mistake:
- 3. Inadequate Substrate Preparation
- Sublimation Mistake:
- 4. Improper Color Management
- Sublimation Mistake:
- 5. Sublimating on Incompatible Materials
- Sublimation Mistake:
- Conclusion
- FAQs (Frequently Asked Questions)
Sublimation printing has become increasingly popular for creating vibrant and durable designs on various substrates, from apparel to promotional items. However, mastering the sublimation process requires attention to detail and a good understanding of potential pitfalls.
In this blog post, we'll explore the top 5 common sublimation mistakes and provide effective solutions to ensure successful and high-quality prints.
1. Poor Image Quality
This heading addresses the common sublimation mistake of using images with low resolution. When the source image lacks the necessary detail, the resulting prints may appear blurry or pixelated, negatively impacting the overall quality of the final product.
Sublimation Mistake:
Starting with a low-resolution image can result in blurry or pixelated prints, diminishing the overall quality of the final product.
Solution:
The solution involves emphasizing the use of high-resolution images, recommending professional graphic design software for image enhancement. And advocating for pre-flight checks to ensure that the image quality meets the required standards before the printing process begins.
High-Resolution Images: Use images with a minimum resolution of 300 dpi for crisp and clear prints.
Professional Software: Invest in professional graphic design software to enhance and optimize your images.
Pre-Flight Checks: Before printing, perform pre-flight checks to ensure the image quality meets the required standards.
2. Incorrect Heat Press Settings
This heading focuses on the potential pitfalls associated with improper temperature, time, or pressure settings on the heat press during the sublimation process. Incorrect settings can lead to issues such as uneven transfers, color discrepancies, or even damage to the substrate.
Sublimation Mistake:
Incorrect temperature, time, or pressure settings on the heat press can lead to uneven transfers, color discrepancies, or even damage to the substrate.
Solution:
The solution involves following manufacturer guidelines for both sublimation paper and substrate, conducting test runs on scrap materials to determine optimal settings. Using a reliable heat press with accurate temperature control to prevent overheating or underheating.
Follow Guidelines: Adhere strictly to the manufacturer's guidelines for both the sublimation paper and the substrate.
Test Runs: Conduct test runs on scrap materials to determine the optimal settings for each substrate.
Reliable Equipment: Use a reliable heat press with accurate temperature control to prevent overheating or underheating.
3. Inadequate Substrate Preparation
Inadequate preparation of the substrate before the sublimation process can result in problems such as uneven color distribution or incomplete transfers. This heading addresses the importance of ensuring that the substrate is clean, dry, and free from contaminants.
Sublimation Mistake:
Neglecting proper preparation of the substrate can result in uneven color distribution or incomplete transfers.
Solution:
The solution includes emphasizing cleanliness, pre-pressing the substrate to remove moisture and wrinkles. Using a lint roller on fabrics to eliminate loose fibers that might interfere with the transfer process.
Cleanliness: Ensure the substrate is clean, dry, and free from any contaminants before starting the sublimation process.
Pre-Pressing: Pre-press the substrate to remove moisture and wrinkles for better ink absorption.
Lint Removal: Use a lint roller on fabrics to eliminate loose fibers that could interfere with the transfer.
4. Improper Color Management
This heading deals with the mistake of inconsistent or inaccurate color management during sublimation printing. Issues in color management can lead to prints that deviate from the intended colors, causing dissatisfaction with the final product.
Sublimation Mistake:
Inconsistent or inaccurate color management can lead to prints that differ from the intended colors.
Solution:
The solution involves regular monitor calibration to ensure accurate color representation, using ICC profiles provided by sublimation ink and paper manufacturers. Performing color tests and adjustments, and maintaining and replacing color cartridges to prevent color shifts over time.
Monitor Calibration: Regularly calibrate your monitor to ensure accurate color representation.
ICC Profiles: Use ICC profiles provided by your sublimation ink and paper manufacturers.
Color Testing: Perform regular color tests and adjustments as needed to achieve the desired results.
Cartridge Maintenance: Regularly maintain and replace color cartridges to prevent color shifts over time.
5. Sublimating on Incompatible Materials
This heading highlights the error of attempting to sublimate on materials that are not suitable for the sublimation process. Substrates that are incompatible can result in poor adhesion and durability issues, affecting the quality of the final printed product.
Sublimation Mistake:
Attempting to sublimate on materials that are not suitable for the process can result in poor adhesion and durability issues.
Solution:
The solution includes verifying substrate compatibility, sticking to polyester-based or specially-coated substrates designed for sublimation. Avoiding materials like cotton that do not work well with the sublimation process.
Material Verification: Verify that the substrate is compatible with sublimation printing.
Specialized Substrates: Stick to polyester-based or specially-coated substrates designed for sublimation.
Avoid Cotton: Avoid sublimating on materials like cotton, which do not work well with the sublimation process.
Conclusion
Avoiding these common sublimation mistakes requires attention to detail and adherence to best practices. By implementing these solutions and regularly refining your process through experimentation and testing. You'll enhance the quality and consistency of your sublimation prints, ultimately ensuring customer satisfaction.
For flawless embroidery results, consider our embroidery services, where our expertise and precision guarantee perfection in every stitch.
FAQs (Frequently Asked Questions)
Q1. What is the recommended minimum resolution for images in sublimation printing?
The recommended minimum resolution for images in sublimation printing is 300 dpi for crisp and clear prints.
Q2. How can one ensure optimal heat press settings during sublimation printing?
Follow manufacturer guidelines, conduct test runs on scrap materials, and use a reliable heat press with accurate temperature control to ensure optimal settings.
Q3. Why is cleanliness crucial in substrate preparation for sublimation printing?
Ensuring the substrate is clean, dry, and free from contaminants is crucial to prevent issues like uneven color distribution or incomplete transfers.
Q4. What role do ICC profiles play in addressing color management issues in sublimation printing?
ICC profiles, provided by sublimation ink and paper manufacturers, help ensure accurate color representation in the printing process.
Q5. Why is it essential to verify substrate compatibility in sublimation printing?
Verifying substrate compatibility ensures that the material is suitable for sublimation, preventing poor adhesion and durability issues in the final printed product.